解決壓鑄粘模缺陷的具體措施
1 壓鑄件粘連的原因
粘模缺陷對鑄件的危害是:壓鑄件粘在模具上時,較輕的表面較粗糙,影響外觀的粗糙度; 重鑄件表面剝落、缺肉、拉傷、裂紋,還會造成鑄件漏水,造成鑄件成批報廢。 壓鑄粘連現像有很多,粘連的基本原因如下。
1.1 壓鑄合金與模具鋼的親和力
壓鑄合金與模具鋼的親和力越大,就越容易相互熔化和結合。 壓鑄合金與模具壁結合後,脫模阻力較大,脫模時鑄件拉緊。 肉眼觀察鑄件粘連部分有表面粗糙、剝落或缺料等拉絲痕跡(注意:與積碳相區別),粘連嚴重時鑄件會撕裂損壞。 型腔表面目視貼合層狀鑄造合金,顏色為白色。
壓鑄合金液體的注入或流動衝擊模具壁或型芯後,模具壁或型芯的溫度升高。 在高溫下,合金液與模具壁的模具鋼熔化並熔合在一起,導致相互粘連。 合金液溫度越高,注射速度越高,模具溫度越高,模具硬度越低,鋁合金液與模具鋼的親和力越高,越容易熔化和焊縫粘連。 當粘附在壓鑄合金上的模具表面脫模時,型腔表面和鑄件表面受到擠壓和撕裂,會撕裂鑄件表面,鑄件表面會出現粘模應變。
內流道中壓鑄合金液的填充速度越高,金屬液流動對模具壁的影響就越嚴重。 熔融金屬直接撞擊芯部或壁部,撞擊力轉化為熱能。 不僅合金液的溫度會升高,受衝擊部位的模具溫度也會升高很多,大大增加了鋁合金液與模具鋼的親和力。 因此,模具中流道受合金液高速沖擊的部位最容易發生粘模。 如果撞擊定模側面,則鑄件在定模側面的保壓力增加。
模具硬度不足,脫模時模具表面會被壓鑄合金擠壓變形,或模芯彎曲變形,從而增加模具對鑄件脫模的抵抗力。
模具材料使用不當,模具溫度高時,壓鑄合金容易粘附在模具表面。
1.2 脫模角度
模具脫模斜度太小(或無脫模斜度,或反脫模斜度),模具側面不平(沖蝕、擠壓、缺陷等),表面粗糙等,鑄件受阻脫模方向。 鑄件脫模時鑄件表面受鑄型拉傷,鑄件表面沿開模方向呈線狀應變痕,即鑄件深型腔開始處的傷痕較寬且深,而模具末端的疤痕逐漸變小甚至消失。 拉緊整個臉。
- (1)模具設計製造不正確,定型型腔或型芯成型面脫模斜度太小或有倒斜度,使鑄件脫模阻力很大。 對鑄件不需要脫模傾角的部位,最好給鑄件留出加工餘量使脫模傾角,然後讓鑄件沒有脫模傾角的部位精加工。
- (2)型芯或型壁的壓碎變形和型腔側面的突起會影響鑄件的脫模,成型面的划痕或結晶器開裂也會影響鑄件的脫模.
模具固定成型面太粗糙,或有加工製造痕跡,不夠光滑,或加工拋光痕蹟的線條與脫模方向不一致,或脫模方向平整度差,這樣的不良表面會增加由於脫模阻力阻礙鑄件脫模,導致鑄件表面有拋光或划痕的痕跡。 此類划痕為脫模方向的線狀凹槽,淺的小於0.1mm,深的約為0.3mm。
1.3 鑄件對模具的密封性
鑄件整體或局部收縮對模具的鎖模力過大,或鎖模力分佈不平衡、不合理。 此時鑄件會因粘模而變形、開裂或斷裂,甚至鑄件會粘在定模上。 或者會出現鑄件粘在動模頂部出不來的現象。
- (1)鑄件對定模的整體或局部保壓力大於對動模的保壓力,鑄件在開模時會卡住。
- (2)脫模時,如果鑄件各部分在動、定模上的緊固力不均勻,拉出時鑄件會偏斜、歪斜、歪斜,鑄件有定模上的大鎖緊力會受到影響。 它可能會粘在固定模具上。
- (3)如果定模溫度過低或動模溫度過高,鑄件收縮時定模的保壓力會大於動模的保壓力。
- (4)脫模劑濃度過低,脫模劑脫模性能不好,定模噴灑脫模劑不到位,脫模劑用量不足,都會影響脫模效果鑄件的脫模性能。 如果在熱模過程中在定模上噴塗太多油漆,定模溫度很難快速升高。 鑄件冷卻收縮後,定模側的鎖緊力會比動模增加更多。
- (5)還有粘模現象:在壓鑄生產的第一階段,即熱模低速注射時,由於壓鑄合金液的流動性會迅速下降。模具溫度低,導致填充型腔內的金屬液成型很不完全,成型的鑄件強度很低,鑄件各部分之間的連接很弱。 鑄件脫模時,擰緊力較大的部分很容易與其他部分斷裂。 分離並卡在模具中。 尤其是定模側面沒有頂針頂出鑄件,更容易粘在定模上。
對於壓鑄過程中每次都會出現的粘連現象,應詳細分析其發生的原因。 比如壓鑄時鑄件粘在定模上,就要檢查鑄件對定模的緊固力過大的原因; 檢查鑄件定模側的外觀,沿脫模方向,鑄件表面是否有模具痕跡。 當粘模嚴重劃傷或劃傷時,脫模阻力大,使鑄件的一部分或整個鑄件出不了型腔,鑄件會卡死,造成粘模; 在嚴重的情況下,不僅鑄件會被撕裂和損壞,在模具的型芯和型腔中還可能出現應變、裂紋、斷裂等現象。 壓鑄件的粘連現像在鋁合金中最為常見。 解決壓鑄件粘連缺陷的具體措施如下。
2 防止鑄件粘在定模上的措施
2.1 壓鑄模具中防止鑄件粘在定模上的措施
在新製作的模具試模中,或壓鑄生產開始熱模時,經常出現壓鑄粘模現象。 當壓鑄操作過程正常時,鑄件粘連的主要原因不是壓鑄過程,而應該是鑄件結構設計、模具設計或製造的問題。 壓鑄工藝和噴塗調試雖然可以補救,但補救效果一般,不是很穩定,仍會出現鑄件粘連現象。
如果鑄件容易粘在定模上,壓鑄前應將模具預熱好,在開始低速注射前,應在模腔內塗上防粘模膏和壓縮空氣。 吹均勻,每個壓鑄模具噴一次,試壓鑄約20個模具,如果模具還是不動,說明模具有問題,需要修理。
對於已經設計好的鑄件,確實鑄件對定模的鎖模力大於對動模的鎖模力。 需要讓鑄件設置在定模一側才能頂出鑄件,並允許鑄件表面在定模一側。 留下頂出痕跡,或使頂出痕跡易於去除。 這樣,在設計模具時,鑄件的頂出機構應設計在定模一側。
注意動、定模保壓力的計算。 對於定模保壓力大於動模保壓力的鑄件,或定模保壓力與動模保壓力相近的鑄件,可以粘住。定模可能會粘在動模的鑄件上。 在設計鑄件或模具時,需要改變鑄件或模具的結構、脫模斜度、表面粗糙度等,並儘量使動模的鑄造力大於定模的緊固力。模具。
對於定模一側保壓力較大的鑄件,在設計新模具時,分型面應盡量選擇在偏向定模的一側,鑄件應置於盡可能多地移動模具型腔,以增加鑄件的配對。 動模的鎖緊力。 為減小對定模的鎖緊力,需與鑄件設計人員重新確定定模的脫模斜度,並儘可能增大定模的脫模斜度; 特別注意修正或增加定模側鑄件。 因模具粘在模具上而拉緊的零件的脫模斜率。 同時,適當減小動模的脫模斜度; 特別注意修正或減小頂針附近動模的脫模斜度。 盡量在動模上設置型芯,或在動模一側增加型芯的長度。
必須防止定模在製造和拋光過程中產生影響脫模的咬邊或粗糙表面; 試模後或壓鑄過程中,需修正固定模腔因壓壞、碰傷而變形; 使用拋光或化學清洗劑清除合金 如果定模表面的粘連痕跡和模具上的合金附著物不及時清除,時間長了粘連現象會越來越嚴重; 更好地打磨固定模腔側壁的粗糙面。 但定模打磨成鏡面後,不利於油漆的附著。 開模時,鑄件與模具之間會產生緊密的真空間隙,增加脫模阻力,因此定模深腔底部不能拋光成鏡面。 . 對於已經氮化過的模具,拋光要小心,防止損壞表面的氮化層,防止越拋光越粘模具。
修改模具流道,適當改變流道的位置、尺寸和填充流向,以消除或減少因流道對定模的衝擊而產生的沖蝕和粘模缺陷。 例如:
- ①改變鋁液的填充流動方向,盡量減少金屬液對定模型腔的猛烈衝擊。 可以改變熔融金屬的直接衝擊斜面向芯部或壁部;
- ②適當增加內流道截面積。 為降低內流道內金屬液的流量;
- ③改變內流道位置,使內流道處於鑄件寬厚位置,避免對定模側壁的衝擊;
- ④盡量取鑄法深型腔底部的進料;
- ⑤採用開放式流道,流道喇叭口面向型腔,增大注射面積;
- ⑥對於流道的衝擊部位或型芯,可用碳化鎢棒塗裝機在模具表面通電。
火花冶金法噴塗碳化鎢微粒層,金屬鎢微粒和母材不會脫落,可提高模具表面的抗粘性能,如在表面沉積2~4微米厚的塗層壓鑄模具的硬度可達HV4 000~4 500,工作溫度可達800℃。
為了將鑄件拉到動模一側,可以從頂出桿的頭部修一個楔形倒鉤鉤(鉤長5-8毫米,鑄件厚度1-2毫米) ,見圖1),使壓鑄倒鉤把手將鑄件拉到動模一側,然後取下鑄件上的倒鉤。 為增加鑄件在動模上的緊固力,對於鑄件上需要精加工的零件和不影響外觀的零件側面,可增加相應模具零件的表面粗糙度質量,以增加鑄件對動模鎖緊力的影響。 更明顯。
為增加動模的鎖緊力,可適當使用拉桿(見圖2):
- ①在不影響鑄件外觀的情況下,可在動模側面或型芯表面開若干凹槽,或在模具內磨若干深度約0.1~0.2mm的凹痕. . 但要注意在頂出桿附近開鉤槽,防止頂出力不均;
- ②開模時,若想用流道將鑄件通過內流道拉到動模一側,可修修動模側流道側的張力筋,或打磨0.2 的幾個深度。 ~0.3mm的凹點,增加流道對動模的鎖模力;
- ③也可以在靠近內流道的流道上設置頂針,將頂針縮短至低於模具表面5-8mm,將頂針低於模孔3mm的一側修整為2mm寬至3毫米,深度為0.3~0.5毫米的環形槽。 壓鑄後形成的環形拉筋帶動流道,流道通過內流道將鑄件拉向動模一側。 更好的結果;
- ④如果是由於澆道襯套對餅塊和澆口施加較大的拉力,將鑄件帶入定模,可在動模流道和分體澆道側修補抗拉筋錐體。 開模時用拉桿將流道和蛋糕拉到動模一側;
- ⑤對於壁厚比較厚的鑄件,或有內孔需要精加工的鑄件,在降低動模芯脫模斜度後,如果不能解決定模問題,可以在型芯中間長度 修一條寬2~3mm、深0.2~0.5mm的環槽,形成拉筋,環拉筋將鑄件拉向動模一側。 請注意,在這樣的型芯附近必須至少有 2 個頂針來頂出鑄件,以防止鑄件變形。
對於定模側保壓力大於動模側保壓力的鑄件,為了使鑄件順利脫出定模,設計了頂出板、頂出桿和復位桿頂出。像活動模具一樣鑄造。 可以在定模一側加裝油缸或彈簧,推動定模上的頂板和頂出桿,在開模的同時頂出鑄件。 頂出板後面有一個彈簧。 開模時,定模頂出器從分型面頂出。 合模時,利用動模分型面推動四個複位桿推動定模推板和頂出器復位。
為了使用頂出桿將鑄件從定模中頂出,也可以使用類似於三板兩件式分型模的鉤桿、衝擊塊和滾輪機構(見圖5,鑄件、頂出桿和復位桿在圖中未示出),依靠開模動作帶動定模頂出推板將鑄件從定模中頂出。 其結構如下: 設計頂針頂出結構,用於給定模具頂出鑄件,讓定模頂出板5伸出定模6外,並在上面設置四個(或兩個)掛鉤動模1.合模時,四根(或兩根)勾桿4伸向定模6一側。 鉤桿4、衝擊塊7、彈簧3、滾輪機構8用於使四根鉤桿4與定模模具的頂推板用鉤子連接。 開模時,動模拉桿4勾住定模頂桿5,定模頂桿推動頂桿5移動頂桿,將鑄件從定模中頂出。 此時鑄件和動模同步運動。 移動到一定行程後,利用衝擊塊、滾輪、彈簧機構將四根鉤桿的鉤子從定模頂出推板上脫開,定模頂出推板停止運動,動模分型面也可在模具閉合時使用。 將四個複位桿推回定模頂出推板,使定模頂出複位。
2.2 壓鑄過程中防止鑄件粘在定模上的措施
模具上的噴塗層、合金液的流動衝擊速度、模具溫度是影響鑄件粘連的主要因素。
脫模劑的種類、質量、濃度、噴塗位置、噴塗時間、脫模劑用量等都會影響鑄件的粘著狀況。 使用噴灑脫模劑的量來調節鑄件在動、定模兩側的脫模效果。 為防止鑄件粘在定模上,可適當減少噴在動模上的脫模劑的時間和用量。 噴在動模上的油漆要薄而均勻,但油漆不能漏。 增加定模脫模劑的噴塗量,以降低模具表面的溫度,特別是定模拉傷的鑄件表面和有拉痕的表面,要增加噴塗量。 當固定模具側面沒有固定位置,或沒有模具痕跡時,注意適當增加噴塗量。
在有拉痕的模具表面,壓鑄後噴漆前先塗防粘模膏,使防粘模膏在高溫下燒結到模具表面,使合金液與模具表面之間形成一層較厚的隔膜層,可以更好地起到脫模作用。
適當調節和控制模具溫度。 有必要分析鑄件緊貼模具的應力、模具的溫差與鑄件的收縮、模具溫度與合金收縮與模具緊度的關係。 如果鑄件表面有粘模應變,在保證鑄件表面質量的同時,盡量使用較低的模具溫度。 如果鑄件本身有較大的緊固力,盡量採用較高的模具溫度,這樣可以減少鑄件在脫模時的收縮,即當鑄件還沒有達到較大的緊固力時,就會開始脫模。
相對降低動模溫度,促進鑄件收縮,可以增加鑄件對動模的緊密度; 相對提高定模溫度,降低鑄件收縮率,可以降低鑄件對定模的緊密度。 增加動模冷卻水的流量,可以降低動模的模具溫度; 減少或關閉定模冷卻水的流量,可以提高定模的模具溫度。 一般壓鑄鋁合金鑄件,開模後1~3秒內測量動模型腔表面溫度。 表面溫度不應大於300℃,最好是(240±40)℃; 噴塗後合模前,在1~3秒內測量定型模腔表面溫度,應不低於140℃。
澆注溫度與模具溫度一樣,可以改變鑄件的收縮率和填料的緊密度。 提高澆注溫度和縮短開模時間可以降低保壓力,但會增加合金液與模具鋼的親和力,造成鑄件厚壁部位粘連的可能性。
3 防止鑄件粘在動模上的措施
3.1 壓鑄模具防止鑄件粘在動模上的措施
鑄件粘住動模的主要原因是鑄件對動模的鎖緊力過大,頂出桿頂出力不足。 如果頂出力不夠大,就需要提高壓鑄機頂出油缸的液壓或頂出速度。 如果頂針直徑太小,或頂針數量少,則頂針強度不夠,頂針可能會彎曲或折斷。
如果鑄件粘在動模上的力小,鑄件脫模時應變較輕,或鑄件表面粗糙引起的阻力小,但鑄件頂出時變形,模具粘模部分應拋光、氮化,或增加噴塗脫模劑的量,降低脫模阻力。 . 如果澆注力粘在動模上,脫模時鑄件受力嚴重,鑄件頂部斷裂或脫開,或鑄件被頂出器頂出,應適當增大澆鑄角度。 改進鑄件或模具的設計,消除導致鑄件粘模和影響收縮的不合理結構。
為防止鑄件頂出力不均造成粘模應變,壓鑄機推動頂出板的四根推桿長度必須相同,相差不得大於0.20mm ; 機器推桿與頂出 鑄件頂出桿的位置應平衡合理,不得偏離模腔中心,不得偏離壓鑄件頂出氣缸中心機器。
如果抽芯和頂出設置不平衡,鑄件就會受力不均而偏斜。 如果壓鑄機液壓頂出油缸的推桿長度不一樣,鑄件頂出力不均,或推杆位置佈置不當,鑄件在頂出時會偏斜. 改進措施是:修改模具結構,調整抽芯機構和頂出桿的位置,使鑄件受力均勻頂出,保證鑄件平行均勻推出; 調整頂出機構,壓鑄機推桿的位置和數量(最容易使用4-6個推桿),使模具的頂出桿和鑄件受力均勻; 合理增加頂出桿數量,加大頂出桿直徑,並安排好頂出杆位置,保證頂出平衡。
如果扁平件和薄壁鑄件的變形抗力不足,則應增加頂針的數量和直徑。 也可以在頂針位置加一個小凸台,讓頂針靠在鑄件的小凸台上。 大頂出力區使鑄件受力均勻。
使用優質模具鋼,使模具溫度高時,壓鑄合金不易粘附在表面。 採用優質模具鋼,模具表面不會過早形成微裂紋,也消除了粘合金的基礎。
當模具硬度不足或脆性時,合金液容易發生粘模。 既要檢查模具硬度是否合理,還要檢查熱處理工藝,防止模具鋼變脆。 能承受內流道沖擊的模塊、模具鑲件和所有型芯的硬度比模腔模塊的硬度高HRc3~5。 當模具設計確認沒有問題,鑄模粘連應變仍難以消除時,必須採用滲氮、KANI 7C、鎢塗層、PVD納米鍍鈦等表面處理措施來改善表面模具的硬度。
對於型腔表面,一般用油石和砂紙打磨。 如果使用氣動工具對粘著部分進行拋光,一定要注意不要損壞模具,以免損壞模具表面的氮化層,否則越拋光,模具越粘。 案件。 清潔粘模或粘布的非空腔部分時,可以用抹刀去除凹凸,然後用砂紙輕輕打磨。 不要把坑挖出來,否則會造成更嚴重的粘連。 注意不要隨時用鑿子清理模腔內的粘模,以免挖傷模腔。
3.2 壓鑄過程中防止鑄件粘在動模上的對策
降低壓鑄機的高速注射速度,或增加模具中流道的面積,適當降低流道的填充速度。 如果在不提高內流道填充速度的情況下增加內流道面積,可以縮短填充時間,減少內流道沖擊產生的總熱量,起到降低衝擊的作用可以實現內流道的。
適當降低鑄造壓力:對於薄壁件和無氣孔要求的鑄件,可選擇較小的壓力,如40-55MPa; 一般鑄件選用55-75MPa; 對於厚壁件和有氣孔要求的鑄件,使用較高的壓力,如75~100MPa; 當必須使用大壓力時,可選擇100~140 MPa。 澆鑄壓力越高,鑄件的機械性能越好,鑄件與模具的緊密度越大。 如果發生粘模,需要確認使用合適的鑄造壓力。 適當減少開模時間(模具冷卻時間),使鑄件在較高的溫度下脫模,模具的合模力未達到最大值,可減少鑄件對模具的合模力,降低模具的粘著。 程度。
如果鑄件的脫模角度太小,最容易造成鑄件粘在模具上。 因此,需要根據鑄件的合金材料和尺寸結構選擇合適的脫模角度。 發生粘模時,適當增大脫模斜度可以消除熱衝擊和收縮引起的粘模現象。 如果鑄件結構不合理,會造成鑄件在收縮和冷卻過程中各部分收縮不均勻,抗收縮不平衡。 如有可能和必要,改進鑄件的設計結構,使壁厚均勻,如改變截面的厚度,厚件盡量設計為空心結構或筋連接結構; 避免厚度差異大的過渡部分; 消除不合理的凸台、凸耳和加強筋。 增大鑄件凹角處的鑄件圓角或脫模角度也可以防止粘模。
在鑄型內流道及合金液充滿衝擊腔的部位、鑄件中壁厚較厚的鑄型部位、鑄件凹角附近,容易受到長時間使用合金液。 鑄件會發生粘連和拉傷,因此模具的這些部位應設置冷卻水管進行水冷。 對於細長型芯冷卻,應增加冷卻水的壓力。 這些都可以很好地降低模具溫度,防止模具粘模。
如果壓鑄合金在鑄件表面附著在模具表面,表面會出現一些小氣泡。 對於這種現象,模具表面用砂布和油石打磨,模具反复卡死,不能徹底解決問題。 解決這種粘連比較好的辦法是對粘模表面進行噴丸處理,或者使模具粘連部分的表面寬度為0.2~0.5mm,深度為0.2~0。 5mm的網紋,2~5mm的間隔,可以消除鑄件表面粘連的缺陷。
流道的收縮導致鑄件變形和粘模。 應加長分流道長度,減少分流道面積; 應減少流道寬度,加長流道長度,減少流道。 通道數; 增加冷卻水對結晶器流道的冷卻,以消除流道收縮對鑄件的影響。
壓鑄鋁合金含鐵量越少(如<0.6%),鋁合金液與模具鋼的親和力越大,越容易粘在模具上。 適當增加鋁合金液的鐵含量,可以更好的降低鋁合金對模具的附著力; 一般要求壓鑄鋁合金液中的鐵含量控制在0.6%~0.95%。 必須防止與低熔點金屬混合引起的模具粘連。 使用母合金調整化學成分時,除鎂、鋅等個別金屬外,不能在鋁液中加入純金屬,防止嚴重偏析造成粘模。
壓鑄合金的收縮率越大,不僅越容易粘在模具上,高溫強度也越差。 有些合金的收縮率較大; 合金的液相和固相溫度範圍越寬,合金的收縮越大。 根據鑄件的結構形狀和復雜程度,如果收縮引起的粘模變形難以消除,可考慮改用體收縮和線收縮小、高溫強度高的合金; 或調整合金成分(如鋁)。 當矽合金中的矽含量增加時,鑄件的收縮率變小)以降低收縮率; 或對合金進行改性,在鋁合金液中加入0.15%~0.2%的金屬鈦等晶粒細化劑,以降低合金收縮的傾向。
4結論
壓鑄件粘連的原因有很多,解決粘連的措施也各不相同。 文章具體提出了解決壓鑄件粘連缺陷的措施。 要仔細觀察分析粘連原因,有針對性地採取措施。 相應的對策可以有效解決粘模問題。
轉載請保留本文出處和地址: 解決壓鑄粘模缺陷的具體措施
明和鑄造公司致力於製造和提供優質、高性能的鑄件(金屬壓鑄件範圍主要包括 薄壁壓鑄,熱室壓鑄,冷室壓鑄),圓形服務(壓鑄服務,數控加工,模具製作,表面處理)。任何定制的鋁壓鑄件、鎂或 Zamak/鋅壓鑄件和其他鑄件要求歡迎與我們聯繫。
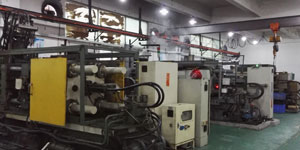
在ISO9001和TS 16949的控制下,所有工藝都通過數百台先進的壓鑄機、五軸機等設備進行,從噴砂機到超聲波清洗機。 銘禾不僅擁有先進的設備,而且擁有專業的由經驗豐富的工程師、操作員和檢驗員組成的團隊,使客戶的設計成真。
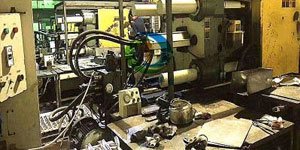
壓鑄件的合同製造商。 能力包括從 0.15 磅起的冷室鋁壓鑄件。 至 6 磅,快速更換設置和加工。 增值服務包括拋光、振動、去毛刺、噴丸、噴漆、電鍍、塗層、裝配和工具。 使用的材料包括合金,例如 360、380、383 和 413。
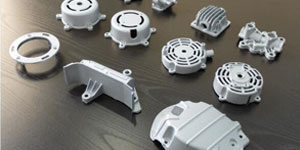
鋅壓鑄設計協助/並行工程服務。 精密鋅壓鑄件的定制製造商。 可製造微型鑄件、高壓壓鑄件、多滑塊模具鑄件、常規模具鑄件、單元模具和獨立壓鑄件和型腔密封鑄件。 鑄件可製造的長度和寬度最大為 24 英寸 +/-0.0005 英寸公差。
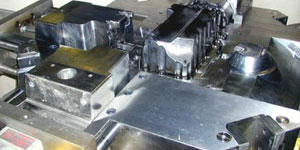
ISO 9001: 2015 認證的壓鑄鎂製造商,能力包括高達 200 噸熱室和 3000 噸冷室的高壓鎂壓鑄、模具設計、拋光、成型、機加工、粉末和液體噴塗、具有 CMM 能力的完整 QA ,組裝,包裝和交付。
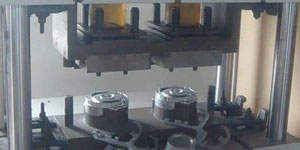
鑄造行業 零件案例研究:汽車、自行車、飛機、樂器、船隻、光學設備、傳感器、模型、電子設備、外殼、時鐘、機械、發動機、家具、珠寶、夾具、電信、照明、醫療設備、攝影設備、機器人、雕塑、音響設備、運動器材、工具、玩具等。
我們接下來可以幫助您做什麼?
∇ 前往主頁 壓鑄中國
By 明和壓鑄製造商 |分類: 有用的文章 |材料 標籤: 鋁鑄件, 鋅鑄件, 鎂鑄件, 鈦鑄件, 不銹鋼鑄件, 黃銅鑄件,青銅鑄件,鑄造視頻,公司歷史,鋁壓鑄件 |評論關閉