稀土氮化工藝的應用現狀及發展趨勢
1980年代中期以來,在生產中,一些一般採用合金鋼滲碳淬火工藝處理的齒輪,具有較高的強度要求,以及高速、大功率、高可靠性的要求。 但滲碳淬火處理後的鋼材形狀比較大,需要增加磨齒處理等後續步驟。 非漸開線齒輪要實現磨齒處理並不容易。 此外,近年來航空航天工業的快速發展也促進了大型精密環件和薄壁件的應用。 目前,這些鋼件的表面處理大多采用滲碳淬火工藝,也存在最終加工成型困難,淬火後變形大的問題。 與滲碳工件相比,滲氮後的工件變形較小,可以較好地解決上述問題。
作為最常見的兩種表面硬化熱處理工藝,滲氮和滲碳各有優勢。 滲氮層的耐磨性比滲碳層好,硬度更高,但工藝週期比滲碳層長。 滲氮層比滲碳層淺(0.3~0.5mm),承載能力和衝擊載荷能力較弱。 . 實驗研究表明,深滲氮(>0.55mm)處理可以部分替代滲碳工藝,還可以有效提高滲碳層的抗衝擊能力和承載能力。
自從稀土應用於化學熱處理以來,國內外學者對稀土在氮化過程中的作用進行了大量研究,並取得了顯著成果。 即在滲氮過程中加入稀土,可以有效提高滲層的滲入速度和硬度。 ,使滲層增厚,改善結構,從而具有催化和微合金化雙重作用。 稀土氮化技術的發展取決於其自身的特點,即獨特的電子層結構使其具有很強的化學活性。
在滲氮過程中加入稀土元素有很多優點:一是可以加快滲氮速度; 二是能有效降低滲氮溫度; 第三,可以大大增加設備和工件夾具的使用壽命; 第四,可以提高零件的彎曲疲勞、接觸疲勞強度和耐磨性等。因此,在中國齒輪滲氮中,將稀土元素引入化學熱處理工藝,使工藝提高到一個新的水平,大大提高產品質量,從而早日與國際接軌,增強國際競爭力。
一、常規氮化工藝的應用現狀
滲氮是一種應用廣泛的表面化學熱處理技術。 滲氮工藝的目的是在基本不改變工件自身性能和尺寸的情況下,獲得較高的表面硬度,同時提高耐磨性,提高疲勞壽命。 . 與其他化學熱處理工藝一樣,滲氮工藝包括滲氮介質的分解、滲氮劑中的反應、擴散、相界面反應、滲入的氮元素在鐵中的擴散,以及氮化物的形成。 根據Fe-N合金相圖,滲氮溫度一般低於590℃(氮的共析溫度),滲氮層從表面到內部形成ε相和α相。 由於ε相中氮原子的擴散速度最慢,在滲氮層形成後,ε相會起到屏障的作用,阻礙氮原子的向內擴散。 因此,一般情況下,滲氮一段時間後滲氮層的生長速度會明顯下降。
稀土氮化工藝
2.1 稀土滲氮機理
稀土是鑭系元素和鈧(Sc)、釔(Y)等17種元素的統稱。 這些稀土元素比較活躍,位於鎂(Mg)和鋁(Al)之間。 由於其獨特的特性,它被廣泛應用於許多領域。 也正是由於這些特性,它可以作為熱處理促進劑,用於化學熱處理。 在化學熱處理中,鑭(La)和鈰(Ce)往往是主要元素,因為它們具有4f電子層結構,化學電負性強,如鈰(Ce)-2.48,鑭(La)-2.52,因此,其化學性質相對活躍,進而使其能夠與多種非金屬產生更好的化學協同作用。 哈爾濱工業大學的學者認為,具有特殊電子結構和化學活性的稀土元素可以滲透到鋼件表面。 之所以有諸多優點,是因為稀土元素一旦滲入鋼的表面,其原子半徑比鐵原子的半徑大40%左右,會引起周圍鐵原子晶格畸變,在反過來會增加缺陷密度,即扭曲會產生更多的新缺陷。 晶體缺陷有利於氮原子的吸附和擴散,使填隙原子在畸變區富集。 稀土元素滲入鋼件表面後,短時間內會在鋼件表面形成較高的氮濃度,從而形成較高的氮勢和濃度梯度,使氮原子向內擴散從而使化學熱處理過程明顯加快和細化滲層結構,提高滲層性能。
筆者認為,稀土滲氮率的大幅提高主要有以下幾個原因:
- 稀土元素的滲入使缺陷密度增加,擴散通量J增大,氮原子的轉移係數大大增加。
- 稀土元素的滲入引起表面Fe原子晶格畸變,使表面能增加,從而增加捕獲間隙N原子的吸附能。
- 畸變區大量N原子的富集,增大了氮濃度差,增強了化學能,加快了擴散速度。
2.2.稀土滲氮的特點
稀土在滲氮過程中的催化作用遠大於滲碳,這是稀土滲氮的一個重要特性。 原因是滲氮溫度通常在α-Fe相區,該相區稀土元素的滲透阻力遠小於γ-Fe相區; 此外,稀土滲入量也是影響滲入效果的主要因素。 . 一般來說,滲入量大的滲入效果較好,滲氮時的稀土滲入量比滲碳時多,所以滲氮時的滲入效果更好。
氮化層中氮化物的分佈和形貌是決定氮化層硬度的關鍵。 當氮化物分散分佈時,硬度較高,反之,硬度較低。 在常規氮化工藝中,一般會產生片狀氮化物,氮化物與母相是共聚或半共聚的。 隨著溫度升高,氮化物不斷積累變大,從母相中脫溶,硬度急劇下降。
在稀土氮化過程中,稀土的滲入使氮化物呈現分散不均勻分佈狀態,使自由能急劇上升,成為間隙N原子的陷阱。 同時,可以形成亞穩態的科特雷爾氣團,可以減少那裡的能量。 氮化物的形成以稀土元素為核心,其分佈變得精細分散。 同時,它還呈現出彌散的準球形析出物,從而避免了脈狀結構的產生,也避免了氮化物沿晶界的偏析。 此外,在一定溫度範圍內,氮化物的形貌不會發生變化,其分佈也不會發生變化。 與常規氮化技術相比,稀土氮化技術使氮化層硬度更高,脆性可保持在0~1級。
2.3. 稀土氮化工藝要求
稀土滲氮具有滲氮層硬度較高的特點。 根據這一特性,氮化溫度可提高10~20℃,從而更有效地促進氮化率的提高。 根據大量實驗結果可以發現,在相同溫度下,稀土滲氮只能提高15%~20%的滲入率,但溫度升高20℃後,滲入率提高可以大大增加。 同時,與常規滲氮技術類似,稀土滲氮必須將滲氮的氨分解率控制在合理範圍內,即初期應採用較高的氮勢(Np),然後逐漸降低。 一般採用變溫變滲氮電位的兩端可控氣氛滲氮工藝,在初期降低氨分解率,提高氮電位以滿足加快滲氮速度的要求,大大提高它。
2.4. 稀土滲氮的經濟效益與節能
採用常規滲氮工藝,一般合金結構鋼,當層數需要0.3mm時,保溫時間一般需要30h以上。 滲層要求0.6mm時,保溫時間需90h以上。 在催化劑中加入稀土滲氮後,當普通合金結構鋼需要0.3mm的滲層時,如果在相同溫度條件下可以採用循環保溫滲氮工藝,保溫時間只需14h。 與傳統滲氮工藝相比,保溫時間縮短16h,節省時間53%。 因此,它可以節省40%的電力,減少約35%的氨消耗,減少約35%的廢氣排放。 當穿透層要求0.6mm時,保溫時間可縮短40%左右。
中國是機械製造大國,有數千家企業使用氣體滲氮,主要分佈在機床製造、風電傳動、航空航天設備、模具製造等行業。 預計3000台井式氮化爐(按75kW計算)每年運行100次,每次通電25h每年耗電5.625×108kW•h。 使用稀土滲透劑可使滲透率提高40%,節電2.250×108kW•h,相當於90,000萬噸標準煤,減少CO2排放80,000萬噸。 因此,如果整個行業在氮化過程中採用稀土滲濾技術,將會有更好的“節能減排”效果。
3、稀土滲氮技術的發展
3.1. 稀土氮化的重要性
近年來,隨著世界能源價格普遍上漲,中國經濟發展面臨巨大挑戰。 為此,提出建設創新型節能國家,實現經濟可持續發展的目標,並出台相關措施,降低能耗、節能減排。 及相關政策,實現高效延壽。 根據稀土滲氮工藝的初步試驗可知,稀土催化滲滲可大大縮短氣體滲氮的時間,對不同鋼材表現出不同的催化效果,一般可縮短30%~60%左右。 %,表面硬度也低。 與傳統氮化相比,可提高50~150HV。 初步測算表明,採用該技術將大大降低電耗,預計可降低電耗30%~40%,減少氮化廢氣排放,縮短工時,提高工作效率。 同時鋼件質量大大提高,耐磨性大大增強,表面耐磨性大大增強,在一定範圍內提高強度和硬度,實現高效使用和長壽命. 稀土氮化技術將推動我國氮化工藝的發展。
3.2 稀土氮化的前景
滲氮工藝具有提高零件表面硬度、提高零件耐磨性、提高耐蝕性和抗疲勞性等特點。 可廣泛應用於模俱生產和動力機械行業。 滲氮是機械加工中不可替代的工藝,但滲氮工藝中還存在一些亟待解決的問題。 例如,處理時間太長。 以0.5mm層為例,需要長達50h。 如果加上輔助時間包括計算,其處理時間將達到3到4天。 因此,這會浪費大量的工時、電耗和氨。 為此,今後滲氮工藝的研究重點應集中在以下幾個方面:一是縮短滲氮時間; 二是加深滲透層; 三是降低能耗; 四是向發展綠色經濟方向轉變。
針對我國豐富的稀土資源和稀土氮化工藝的諸多優勢,應通過技術創新和推廣,充分發揮資源和技術優勢,形成產業發展優勢和經濟效益。
材料科學與技術研究人員應以稀土氮化工藝的創新與推廣為研究重點,對其內在規律和氮化機理進行更深入的探討。 持續開展高效稀土催化劑的研發,力爭實現稀土氮化工藝全面替代常規氮化工藝,最大限度發揮節能減排降耗增效效果增加和延長壽命。
轉載請保留本文出處和地址: 稀土氮化工藝的應用現狀及發展趨勢
明和 壓鑄公司 致力於製造和提供優質和高性能的鑄件(金屬壓鑄件範圍主要包括 薄壁壓鑄,熱室壓鑄,冷室壓鑄),圓形服務(壓鑄服務,數控加工,模具製作,表面處理)。任何定制的鋁壓鑄件、鎂或 Zamak/鋅壓鑄件和其他鑄件要求歡迎與我們聯繫。
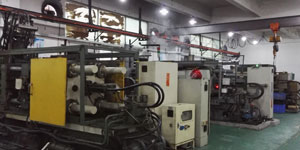
在ISO9001和TS 16949的控制下,所有工藝都通過數百台先進的壓鑄機、五軸機等設備進行,從噴砂機到超聲波清洗機。 銘禾不僅擁有先進的設備,而且擁有專業的由經驗豐富的工程師、操作員和檢驗員組成的團隊,使客戶的設計成真。
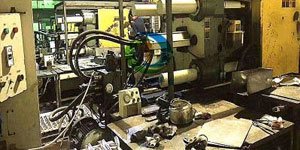
壓鑄件的合同製造商。 能力包括從 0.15 磅起的冷室鋁壓鑄件。 至 6 磅,快速更換設置和加工。 增值服務包括拋光、振動、去毛刺、噴丸、噴漆、電鍍、塗層、裝配和工具。 使用的材料包括合金,例如 360、380、383 和 413。
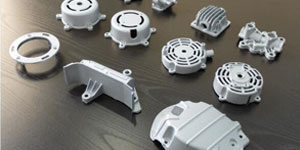
鋅壓鑄設計協助/並行工程服務。 精密鋅壓鑄件的定制製造商。 可製造微型鑄件、高壓壓鑄件、多滑塊模具鑄件、常規模具鑄件、單元模具和獨立壓鑄件和型腔密封鑄件。 鑄件可製造的長度和寬度最大為 24 英寸 +/-0.0005 英寸公差。
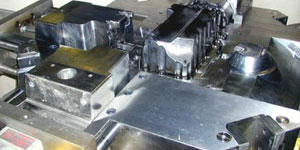
ISO 9001: 2015 認證的壓鑄鎂製造商,能力包括高達 200 噸熱室和 3000 噸冷室的高壓鎂壓鑄、模具設計、拋光、成型、機加工、粉末和液體噴塗、具有 CMM 能力的完整 QA ,組裝,包裝和交付。
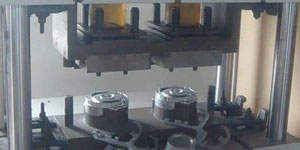
鑄造行業 零件案例研究:汽車、自行車、飛機、樂器、船隻、光學設備、傳感器、模型、電子設備、外殼、時鐘、機械、發動機、家具、珠寶、夾具、電信、照明、醫療設備、攝影設備、機器人、雕塑、音響設備、運動器材、工具、玩具等。
我們接下來可以幫助您做什麼?
∇ 前往主頁 壓鑄中國
By 明和壓鑄製造商 |分類: 有用的文章 |材料 標籤: 鋁鑄件, 鋅鑄件, 鎂鑄件, 鈦鑄件, 不銹鋼鑄件, 黃銅鑄件,青銅鑄件,鑄造視頻,公司歷史,鋁壓鑄件 |評論關閉